Foundation blocks are a unique kind of hollow stone that is filled with concrete and utilized as masonry formwork for elements. You may get more details about this here.
Foundation blocks. Building blocks for a foundation. Broad details
For masonry formwork, shuttering blocks are frequently utilized, particularly for walls that will eventually come into contact with moisture, like basement walls.
See also: Crucial requirements for concrete
See also: Hollow concrete blocks
Moreover, look into sources and solutions for concrete manhole rings.
Like garden wall blocks, shuttering blocks can also frequently be dry-walled and then filled with concrete.
Building blocks for a foundation. Present deals
Blocks of concrete
serrated, 36.5 x 24.5 x 23.8 cm
Block of concrete, 11.5 x 49 x 23.8 cm
Other void stones
Block of pumice, 49.7 x 30 x 23.8 cm
Blocks of expanded clay, 11.5 x 49 x 23.8 cm
building blocks for a foundation. What to look for and suggestions for purchases
Although the terms “foundation stone” and “formwork stone” are sometimes used synonymously, there are differences between the two; therefore, before making a purchase, ascertain what kind of stone you require.
Further details on this subject:
An article on hollow bricks on Wikipedia
For concrete formwork blocks, DIN EN 15435
Bricks and concrete blocks
Foundation blocks. FORMWORKING AND FOUNDATION STONES: ADEQUATE CONCRETE
There are a few guidelines and recommendations that need to be followed when pouring concrete into formwork blocks. It is best to consult an expert for advice.
How can I create my concrete blocks?
Just pour concrete yourself to create slabs and blocks.
Using premium molds from concrete blocks.
This is a cost-effective and useful solution for recycling organizations since they can simply construct halls, walls, or collection boxes using the Lego principle by using casting molds in different sizes and versions. This also holds for recycled and leftover concrete.
The motto of Concrete Block, a Dutch supplier, is “no concrete to waste”—from leftover concrete to the final product!
Foundation blocks. Make blocks of concrete.
It is advised to use a level and even cast iron plate with a thickness of around 20 millimeters as the substrate for the completed casting mold. Concrete is poured into the mold and the floor after formwork oil has been put into them. After a little while, the concrete is vibrated and the surface is smoothed.
Using the opening key, the mold is simple to disassemble after the concrete has solidified. After that, the completed concrete block is placed sideways and needs to be oriented vertically. For this use, Betonblock has created a rotator. The pictures (down below) show each step of the creation process.
It is safe to stack concrete blocks on top of each other because of the top knobs, bottom recesses, and weight of the blocks themselves. For this, mortar is not needed. Requests for extensions and modifications are always welcome. In actuality, bulk containers, hallways, walls (including fire barriers), fences, and even counterweights for construction cranes are built using stackable, space-saving concrete blocks. Additionally, in the building of roads and other infrastructure projects. Sheds and warehouses can also be constructed with concrete blocks. Of course, concrete is subject to stricter regulations.
Several dimensions
There are several dimensions available for concrete block molds. The application and intended area of application are determined by the concrete’s quality, size, and weight of the poured concrete block. It is possible to make half blocks of concrete in addition to single blocks using a typical concrete casting mold. There are also wall steps and insert pieces available for sloping walls with a 45 degree inclination. They don’t need a separate mold, and they are simple to (de)assemble. Furthermore, Betonblock provides casting molds for 45-degree pitched roofs in addition to molds for casting corners at angles ranging from 90 to 180 degrees. Molds can be used to create more aesthetically pleasing constructions.
Make slabs of concrete
As a substrate, an iron plate is also advised. The work steps that follow closely match those involved in making concrete blocks. For both temporary and/or permanent paving, concrete slab molds can be used to pour a sturdy and solid concrete slab.
For example, sewage is always available from below ground. The largest loads are successfully withheld by concrete slabs. Extreme weather and even big point loads are no problem. The concrete slabs may be lifted as they fall, which is an advantage over a poured surface in the event of a less stable substrate.
Many businesses use their factories to make all of their casting molds. They are composed of structural steel with a long service life that is of excellent quality and low alloy, powder-coated. Since the first generation of steel forms became popular twenty years ago, a lot has been developed here. The system of concrete blocks is currently one of the systems with the quickest rate of growth available, serving more than 3,000 clients across 35 countries. All products are in stock at Concrete Block, and they can be sent to any part of Europe in a matter of days.
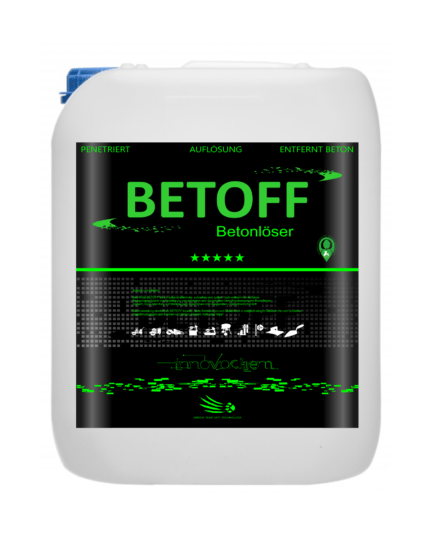