Concrete with fibers. The use of fiber reinforced concrete allows for the construction of exceptionally sturdy buildings. The composition of regular concrete is altered and its qualities are enhanced for its designated purpose in fiber reinforced concrete by adding mechanical, biological, or mineral fibers. In order to weigh the benefits and drawbacks of various fiber reinforced concrete options, your construction contractor will need to be aware of the following details before making a recommendation for your large-scale building project.
Concrete with fibers. Numerous varieties of fiber-reinforced concrete
Fiber reinforced concrete is chemically quite similar to plain old concrete. Cement, sand, gravel, and water are the usual ingredients, and then different kinds of fibers are added. Ceramic, metal, or organic materials can all be used. To make the mixes more fluid, admixtures are commonly used. Long fibers, measuring 5–60 mm in diameter, are mixed with concrete at a dosage of 0.5–2% by volume, or 5–150 kilogram per square meter. The qualities and benefits of various fiber types are distinct.
Concrete with fibers. Fibres made of carbon steel
Metallic fibers include materials such as cast iron, stainless steel, and steel. The final product, the concrete, has remarkable flexural and tensile strengths. Additionally, the likelihood of cracking is reduced.
The addition of metallic fibers to concrete necessitates a minimum compressive strength class of C30/37. It is forbidden to utilize concrete that contains structural fibers in areas with a moderate to high seismic risk.
Concrete with fibers. Natural materials
Organic fibers include acrylic, aramid, carbon, Kevlar, polyamide, polypropylene, and polypropylene/polyethylene. Reduced early cracking is a benefit of the produced concrete.
Despite its malleability, this concrete type does not have great heat resistance.
The use of fibers in concrete. Metal strands Found in a variety of minerals, including wollastonite, mica, glass, and basalt. Thanks to its high thermal insulation and fire resistance, they make it possible to build very thin walls.
Concrete with fibers. Can you explain how fiber-reinforced concrete is made? Considerations for and against fiber-reinforced concrete
Properties of fiber-reinforced concrete vary with the type of fibers used. But fiber-reinforced concrete is typically more manageable and lighter than conventional concrete. More often than not, it also has superior resistance to fire, wear, impact, abrasion, adhesion, and bending. It also lessens the likelihood of micro-cracks.
In place of bar-reinforced concrete, fiber-reinforced concrete is frequently employed. The higher price tag compared to plain old concrete is one major drawback of fiber-reinforced concrete.
Concrete with fibers. For what does it exist?
Slabs, flooring, facade cladding, and other exterior and interior uses for fiber-reinforced concrete abound. It has a wide variety of applications. You can find it in a variety of forms, including prefabricated segments or beams, poured ceilings and slabs, sprayed wall or facade reinforcement, and mortar for sealing or painting.
Mixed-media construction with fiber reinforcement. Price points and retail outlets
You may find fibre-reinforced concrete from hardware stores, specialty shops, and even on the internet. A 30 kg bag will cost you roughly 90 pounds, and a professionally placed fiber-reinforced concrete slab would cost you around 250 pounds per square meter.
Technology in concrete: fiber-reinforced concrete meeting the most stringent standards
In recent years, concrete technology has been evolving at a continuous pace. Concrete with improved qualities has been manufactured, serving multiple purposes, as a result of study into recipe materials. Modern high-strength concretes include ultra-high-quality fiber-reinforced concrete (UHPC). Because of the fibers included in this concrete, reinforcing is not necessary while constructing buildings.
Mixed-media construction with fiber reinforcement. Features of Fiber-Reinforced Concrete with Extremely High Performance
Crafting Fiber-Reinforced Concrete with Extraordinary Performance Levels
The development of ultra-high performance fiber-reinforced concrete hinges on two main principles: first, improving the granulate’s composition; and second, decreasing the water content to lessen the concrete’s porosity by the use of superplasticizers.
The size and kind of grains are actually carefully studied at the onset to reduce air spaces that could damage the concrete. Various sizes of grains are used in ultra-high performance fiber-reinforced concrete. When making concrete, smaller grains are better for achieving compactness.
The remaining metal fibers, which make about 2–3% of the volume (160–240 kg/m3), have a diameter of no more than 0.3 mm.
Concrete with fiber reinforcement
Features of Fiber-Reinforced Concrete with Extremely High Performance
Using ultra-high-performance fiber-reinforced concrete as a matrix makes the cementitious material very robust. Compression resistance (130–250 MPa) and tension resistance (5–12 MPa) are major contributors to the increased strength.
The reduced porosity and its related durability. The second characteristic is the ability to withstand shock and chemical assault.
One distinctive feature of ultra-high-strength fiber-reinforced concrete is its ability to undergo deformation without cracking, which is a result of the great tensile strength of the fibers used to manufacture it.
The megapascal (MPa) is a standard for measuring traction and compression. Compression, the force that results from the application of two opposing forces, causes an item to be compressed and therefore shrinks in size. The stress that an object experiences when it is stretched is known as tension.
Concrete with fibers. Uses of concrete with extremely high-strength fiber reinforcement
The mechanical resistance to tension and compression is exceptionally strong in structures constructed from ultra-high-strength fiber-reinforced concrete. Consequently, this type of concrete is used to construct structures that necessitate compressive strengths above 150 MPa.
As an example, consider the following: the Sherbrooke Footbridge (built in 1997), the Seoul Footbridge (built in 2002), and the Millau Viaduct (built in 2005). You can also use ultra-high-performance fiber reinforced concrete to strengthen or fix some buildings. Plus, compared to conventional concrete, ultra-high-performance fiber reinforced concrete is more costly because of its special formula. This concrete, with its exceptional mechanical qualities tailored to one-of-a-kind constructions, is exclusively produced by concrete plants. The specifics determine the fee that each facility charges.
Lastly, if you are seeking a construction expert with extensive knowledge of fiber reinforced concrete, please share your opinions in the space provided. Once again, we will be in touch with you.
Which product is the best to dissolve concrete with fibers?
For sure it is a BETOFF!
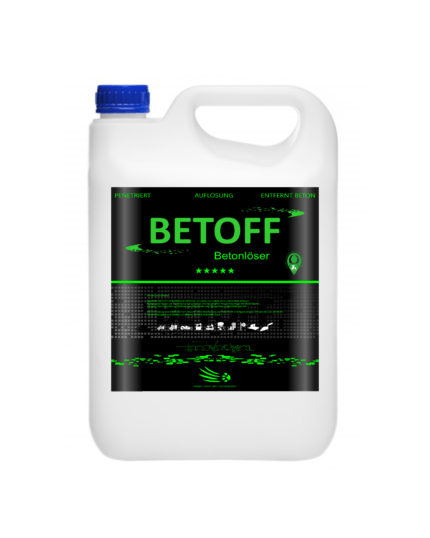
Be sure to read our other articles as well:
- A concrete floor needs a sealant to keep it looking good.
- Concrete Sealant Wood or Concrete for Your Home?
- Top-Rated Concrete Paint and Equipment