Cladding, what is a concrete cladding. With a wide choice of long-lasting textures, colors, and patterns, including a variety of facing materials like stone and brick, precast concrete cladding provides an affordable way to create a sturdy, superior exterior. Architectural precast concrete cladding is another name for it. Self-finished architectural concrete, often known as “Reconstituted Stone” or “Recon,” is made from a carefully chosen variety of natural ingredients and has a more stone-like appearance than regular concrete.
With just-in-time delivery, precast concrete cladding may be swiftly put on site, providing major advantages for both construction and the schedule. Additional advantages include great thermal performance, reduced waste and material efficiency, and quality-controlled and predetermined surfaces.
Panels may be self-supporting and restrained, or they may be supported by a building’s structural frame. In order to support floors, cladding panels can also be made to sustain weight.
Benefits consist of:
- Off-site production: offering resource efficiency through quick construction schedules that are unaffected by bad weather or a lack of labor, low-waste manufacture and installation, and quality control.
- Expert manufacturing and installation: In specially designed factories, panels are made by talented artisans, and teams of experts who have received training in their safe handling and repair install them.
- Quality control: Every manufacturing step is examined in compliance with a quality system that has been independently certified. Before delivery, finish and dimensional accuracy are checked.
- Fast construction schedules: Manufacturing occurs concurrently with the foundation and frame construction, allowing for just-in-time delivery and installation. In the manufacturer, panels might be delivered with windows and insulation installed, which will speed up the work of subsequent trades. Following-on trades might begin earlier when the dry envelope is enclosed early.
Variety of distinctive, aesthetically pleasing options: Custom solutions are offered, and a broad range of finishes, textures, patterns, and forms are possible. - Efficiency of construction: Since fixings are accessible from the back of the panels, external scaffolding is typically not needed. Panel designs can be made to maximize crane delivery and usage.
- Low waste and material efficiency: Because the units are fully engineered in the factory, very little waste is generated during production. Delivery and installation require little to no packing.
- High thermal performance: The thermal mass of an insulated concrete sandwich panel’s internal skin can be used to augment the decomposition delay’s ability to increase internal thermal comfort. Excellent airtightness is provided by concrete panels.
- Good acoustic insulation: Concrete has a high level of acoustic insulation by nature, which makes concrete cladding especially helpful in noisy or crowded metropolitan settings.
- Low upkeep: Compared to alternative lighter-weight cladding options, concrete cladding usually requires less maintenance, which lowers lifecycle costs.
Fire resistance and lack of flame spread: Concrete cladding provides exceptional natural fire resistance, shielding residents from the effects of outside fires. - Adaptability and longevity: Concrete cladding produces long-lasting facades. They can also be easily disassembled, with panels that may be crushed to produce scrap steel and recycled aggregate or even rehabilitated for additional use.
Create and produce
Most panels used in the UK are produced in the UK or Ireland, where producers provide a variety of services and output levels.
It is advised to have an early conversation with cladding manufacturers in order to increase cost efficiency and get expert input on the design development. A reasonable first guess is that the concrete is 150 mm thick.
Panels may quickly cover enormous spaces since they are usually made to span from floor to floor or from column to column. Panels are fastened to frames using brackets that can be adjusted in three dimensions.
After being hired, manufacturers usually offer design services, creating drawings of each individual unit for coordination, and supply samples of the mix and finish for specifications.
Precast concrete panels, typically composed of fiber glass or wood, are cast face-down in specially designed molds. Additionally, there are highly automated facilities that use movable steel beds as the foundation for custom molds. From elaborate leaf patterns to false joints, a variety of designs and effects can be produced by inserting mats or rods into the mold’s base.
Before the concrete is poured, a steel reinforcing cage—which is intended to satisfy both the final structural requirements and those for moving the element during manufacture and installation—is positioned in the mold. Increasingly, other components, such as windows or insulation, are being fixed during manufacturing to make the most of off-site fabrication.
To obtain a high-quality surface finish, the unit’s exposed surface can be treated in a number of ways once it has been demolded, such as acid-etching, smooth or coarse grinding, grit or sand blasting, rubbing, or polishing.
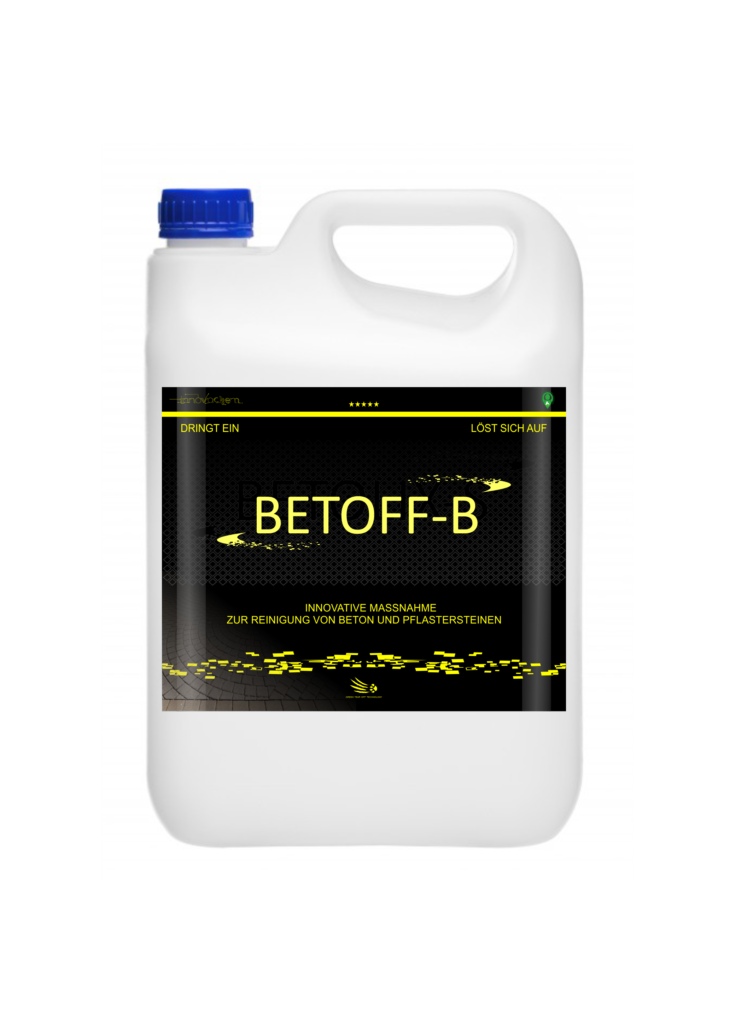